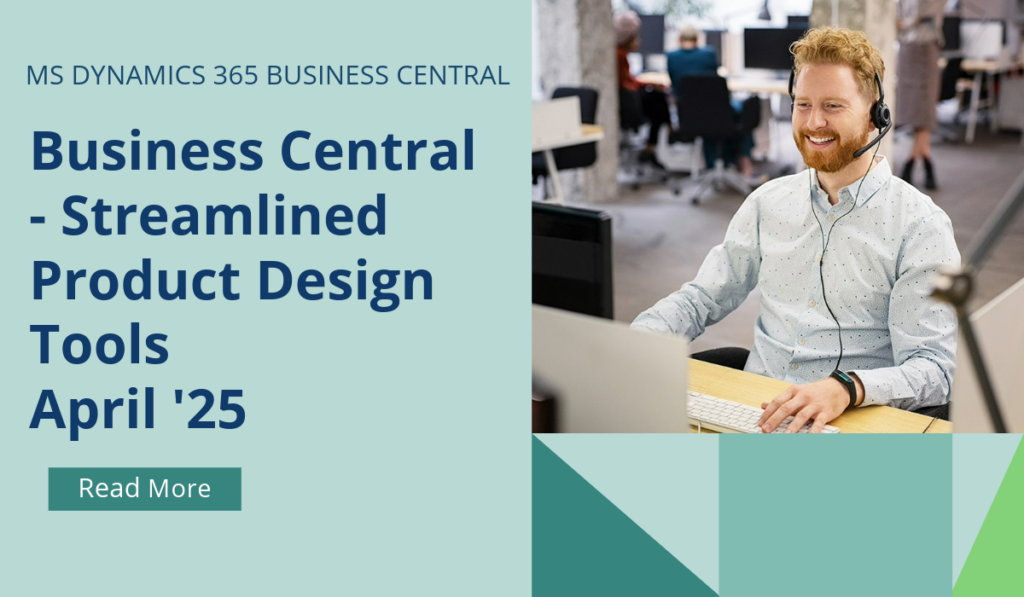
Business Central – Use Streamlined Product Design Tools in Manufacturing
In the world of manufacturing, product design plays a pivotal role in transforming raw materials into finished goods. Production bill of materials (production BOM) and production routing are key concepts in manufacturing. A production BOM lists all components required to produce a product, ensuring accurate assembly and resource planning. Production routing tells us what to do with those components to get a finished product or subassembly.
Manufacturing is a dynamic environment where changes are inevitable. Whether it’s a new component to improve product quality or a shift in supplier, you need to manage updates efficiently to avoid disrupting production. This is where BOM versions come into play. In this release, Microsoft added a number of capabilities to improve the product design stage.
You can save a step by adding multiple items to the production BOM or production order components. When you’re working with a production BOM, production BOM version, or editing components in a planning worksheet or production order, you can use the Select items action to select and add multiple items.
Go to active production BOM version from Item Card and Item list pages
Sometimes companies need to make an adjustment to a production BOM. Rather than create an entirely new production BOM, you can update the current one by creating a version of it. Creating a version lets you keep the original production BOM in case you need it for reference, but use the new version in production. The starting date and status fields define which version to use. In this release, you can easily go to the certified BOM or BOM version that’s valid on the work date by choosing the Prod. Active BOM Version action.
BOM version matrix page includes original BOM as baseline
Use the Production BOM Version Comparison page to view a list of all production BOM versions and items and the quantity used per item. You can use the matrix to compare different production BOM versions concerning the used items per version, including the original BOM as the first column. This functionality ensures clear visibility of all BOM versions and their respective quantities.
The Production BOM Version Comparison page provides better usability and replaces the Prod. BOM Matrix per Version page.
If you’d like to discuss more about Business Central’s upcoming changes, or about making the move across to BC, reach out today to Brookland Solutions for a no obligation discussion. Get in touch!
May 2, 2025
RECENT POSTS
What to Expect from a Business Central Implementation Partner?
You’ve chosen Microsoft Dynamics 365 Business Central as your ERP of choice, and you’re ready to integrate it. But does the next step of implementation feel overwhelming? Even if your current partner has successfully implemented [...]
Enhancing Mobile Access to Business Central for Your Remote Teams
Remote work and hybrid teams are the standard for many businesses. As a result, it’s no surprise that employees are increasingly dependent on their phones and tablets for professional interactions. Whether they’re interacting with customers [...]
5 Signs It’s Time to Replace Your Finance System with Business Central
Chances are, no matter how large your business, there will be a day-to-day need to manage finances, meaning you’re dependent on a financial system. Without an ERP for financial management, your business may struggle to [...]